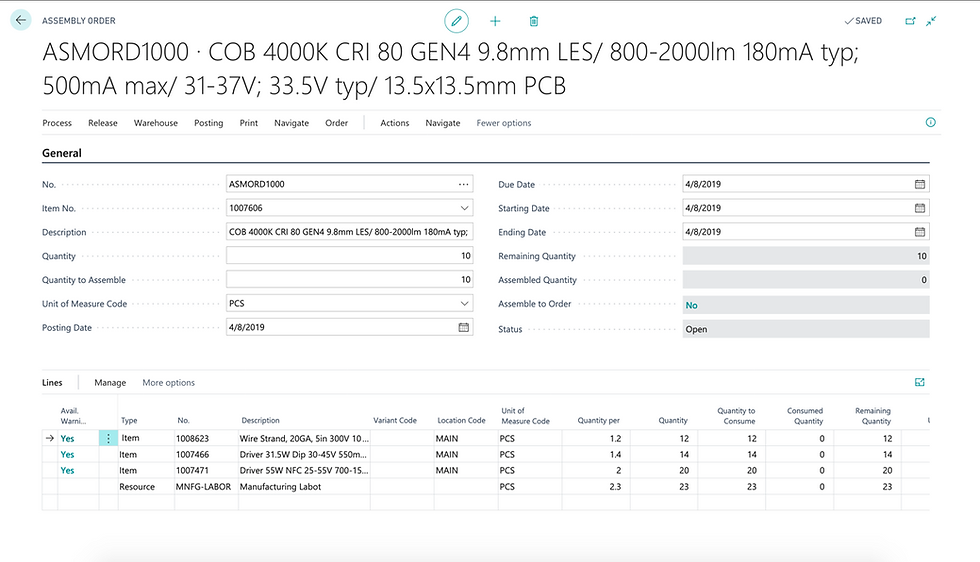
Many of clients in the Manufacturing and Distribution industries are forced to decide which part of the Business Central product is best suited for their needs. In an effort to clarify some of the consideration of system module deployment, please be aware of the following items:
What the modules have in common:
Both Assembly and Manufacturing modules can track single or multi-level Bill of Materials for a finished product
Both modules support a separate transaction to decrease raw materials and increase finished goods with support for Lot Number or Serial Numbers
Both Bill of Materials support non-inventory Resources such as people or machines
Both modules offer the ability to link the Sales order to an assembly or production order in a make-to-order configuration
Both modules have the ability to schedule a start and end date for the transaction
Why would you use the more complicated production modules versus the assembly order process:
Have the ability to track work centers or machine center in routing steps (Process)
Have the ability to track Versions (Revisions) for changes to Routing Steps
Track unit capacities for work centers or machine centers and provide for scheduling options
Support for outsourced routing steps and related transactions (Subcontractors)
Production Bill of Materials supports version tracking (ECM)
Ability to share the same Bill of Material across multiple items
Ability to share the same routing steps across multiple items
Production orders support multiple finished goods or sub-assemblies on the same transaction
Separate the consumption of raw materials from the output of a finished good to provide for accurate inventory for an extended manufacturing process
Support for Scrap Percentage and Safety Stock Settings
Support for back and forward flushing methods for raw materials
Track production orders in different stages including simulated, planned, firmly planned and released production order
Ability to track a Production Journal which includes Consumption journal and routing steps specific output journal entries
Provides the sales team with a simulated production order tool which would provide a delivery date for finished goods based on availability of raw materials, sub-assemblies and machine capacities
It is important to note that Business Central supports a setting of assembly versus production modules selection on an Item-by-item basis. We would be glad to assist in a Consulting Project to review your specific requirements and assist in the proper module implementation for your organization.
The Assembly module is a standard feature of the Business Central Essentials subscription while the manufacturing module is only part of the Business Central Premium Edition. If you select one subscription over the other, the ENTIRE organization has to make the same selection. Business Central does not allow for mixing subscriptions on a user level.
Please call us at Tel. (855) 227-0700 or e-mail our team at Sales@CBRTechnology.com .
Comments